Accommodation Barge and Accommodation Ship
Accommodation Barges are inalienable parts of the offshore industry. These are shallow draft vessels which are moored next to the offshore sites to provide additional accommodation facilities whenever a rig or platform is incapable of fitting all the offshore personnel.
Today these barges are usually equipped with cranes and maintenance equipment so as to perform some offshore construction work as well. But it’s not all work and no play; modern AWBs might be fitted with a bar, cinema, gym, conference rooms and lobby for meetings as well as a swimming pool.
Anchor Handling Tug Supply Vessel (AHTS)
Anchor Handling Tug Supply Vessel (AHTS) is another ship that can be found at any drilling site. AHTS vessel is truly universal as it combines a number of functions: tows rigs and platforms; anchors and moors mobile structures into the position at the site and supplies them subsequently. Big ships are capable of working in deep waters, for instance in Brazil or the Arctic region.
AHTS ships are defined by the required bollard pull, so they have a very distinct design with a big propeller, hull shape that provides the maximum immersion and stability as well as a range of specific deck equipment such as winch, stern roller, etc. However, their most distinctive features are powerful engines with BHP reaching 12240 and more (to compare 25 000 DWT Bulk Carrier will be fitted with a far less powerful main engine of approx. 6946 BHP).
There are usually up to 20 seafarers onboard AHTS vessels. Meanwhile, the crew of AHT ships might be smaller. Anchor Handling Tugs (AHT) are very similar to AHTS and perform the same role, but tend to be smaller and less technologically advanced.
Cable Laying Vessel
Offshore industry doesn’t revolve around oil and gas alone; and Cable Laying Vessels are the best proof of this statement. They are designed for the specific purpose of laying underwater cable networks.
Imagine the level of our dependence on this kind of communication that it proves to be economically sound to build huge vessels devoted to the sole purpose of cables’ installation.
To ensure the maximum efficiency Cable Layers usually can lay the main and auxiliary umbilicals simultaneously. In addition, they are equipped with a profound DP system and both hydraulic and pneumatic cable laying systems.
Crew Boat
Crew Boats are the offshore vessels that are used for transportation of personnel and consumables (water, fuel) when the offshore site is situated within the 200 nautical miles (370 km) distance.
These vessels can differ in size from 30-to-60 ft (9.1 to 18.3 m) to big 200 ft (61m) ships that can transport up to 100 marine specialists. Usually, crew boats are fast (pick up a speed of approx. 33 knots) and have a crew of 4 – 5 seafarers.
The largest crew boat in the world today is catamaran Muslim Magomaev built in 2015. It boasts an overall length of 70 m and travels at a maximum speed of 38 knots.
Diving Support Vessel (DSV)
Today DSVs tend to be one of the most sophisticated offshore vessels. Their role is to provide a base for diving specialists who conduct underwater maintenance or inspections of mobile platforms, rigs, pipelines and their connections, well-heads, etc.
Therefore, DSV is usually fitted with a moonpool (open area in the middle of the vessel where divers’ and ROV’s operations start their operation) and recompression chamber. In addition, Diving Support Vessels always are provided with a DP3 class positioning system due to safety requirements.
Scandi Arctic is reputedly the most technologically advanced DSV these days. She is a saturation dive support vessel equipped with the 24-man diving complex with Hyperbaric Monitoring and Control System.
Saturation diving is used for the most challenging and hard-to-reach offshore jobs requiring to create the pressurised environment filled with oxygen-helium mixture where divers live for the entire contract.
Diving support requires navigational perfection, so Scandi Arctic is DP3 class vessel; and is fitted with advanced National oilwell crane 400t-15m with wire capacity 2000 m to be able to perform some Inspection, Repair and Maintenance (IRM) operations.
Drilling Platform
People drill for oil from the submerged wells from the end of the 19th century. The first such production started in the Grand Lake St. Marys in Ohio in 1891, but the offshore drilling in the form we know (deep wells, semi-submersibles and self-sufficient drilling platforms started only in the mid-20th century).
Jack up rigs emerged in 1954 with the need to drill on the depth more than 30 meters (98ft); while semi-submersible platform was invented by accident in 1961.
Shell had a submersible four-column drilling rig called Blue Water Rig No.1 in the Gulf of Mexico, but its construction was deficient and the pontoons failed to support the weight of the rig sufficiently. Therefore, the rig was towed at a draught midway between the deck and the pontoons. It was noticed that the motions of this draught is very small and it’s more reasonable to operate the rig in this floating mode.
Since that time six generations of semi-submersibles have been developed each generation able to drill in deeper waters. At present the 6th generation operates in waters deeper than 3000 m.
Semi-submersibles use Dynamic Positioning to stay above the well; and anchors in shallower waters; they usually are connected to the ocean floor by umbilicals as fixed structures are not practical in such depths. Whereas fixed drilling platforms operate in less deep waters and are fixed to the shelf.
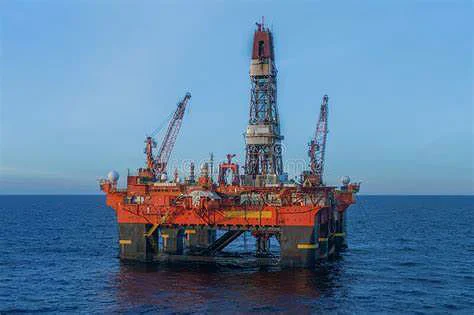
FPSO (Floating Production Storage and Offloading)
An FPSO is a floating unit used in the oil and gas industry for production and storage of hydrocarbons. FPSO are usually chosen for the oil abundant areas located away from the developed pipeline infrastructure.
FPSOs is to produce, process and store oil itself; alternatively, she collects it from the subsea template or nearby rig. The risers that come from the seabed are connected to the special mechanism (turret). The vessel is able to rotate around it to ensure safety or even disconnect temporarily from the subsea infrastructure and sail away to escape severe weather .The first FPSO to obtain such a unique capability was Shell’s urritella. She is stationed in the Stones oilfield in the Gulf of Mexico and is the deepest FPSO in the world operating in a water depth of 2,900 meters (9,500 feet) making her the world’s deepest Oil & Gas production unit of any kind as well.
The world’s largest FPSO is Egina built for the remote Nigerian same-name oil field. She is 330 m long while her storage capacity reaches 2.3 million barrels of oil.
Jack Up Rig
Jack Up drilling platform is rightly considered to be one the most convenient Mobile Offshore Drilling Unit (MODU) in the industry. The era of jack ups has started back in 1954 when Leon B. DeLong in cooperation with McDermott developed the first mobile unit for Humble Oil. It was called DeLong-McDermott No.1 and had 10 legs with spud cans.
Jack ups have been refined into technological masterpieces since that time. Now they are easy to transport (usually by AHTS or Heavy-Lifts), but there are also self-propelled rigs. They are more stable than semi-submersibles and cheaper than FPSO or drill ships. However, its advantages impose certain limitations, i.e. jack up can drill up to the water depth of 107 m (350 ft) only.
Jack Ups differ by the number of characteristics:
- Number of legs (there can be either 3 or 4 ones);
- Legs designs: open-truss legs which are made of crisscrossed tubular steel sections and columnar legs made of immense steel tubes. The latter are cheaper to produce, but can be used up to 76 m (250 ft) water depth because they prove to be less durable.
- Leg support: there can be a mat support that connects all legs and independent-legged rigs with spud like support.
- Drilling device design: the most popular are cantilevered jack-ups where drilling derrick is mounted on the arm placed out of the drilling deck. The other option is the slot-type jack-up. These types have the drilling equipment in the special slot in the drilling deck.
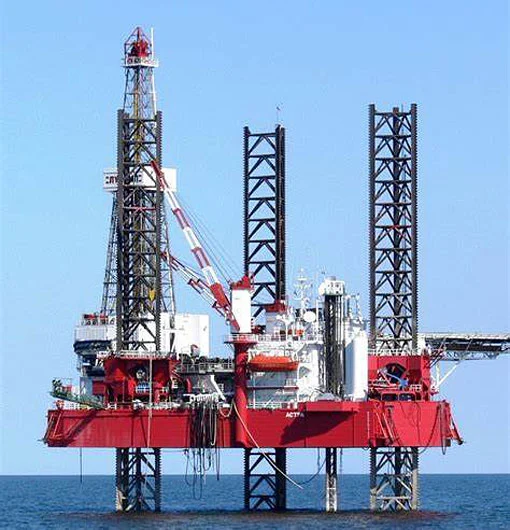
Offshore Construction Vessel
Offshore Construction Vessels (OCV) are huge and technologically advanced vessels used for deep sea and subsea construction or vice versa decommissioning of offshore structures. For instance, OCV might be contracted to build a wind farm, oil platform, take part in a pipe laying project or dismantle a drilling rig.
As a rule, these are DP vessels with heavy-duty cranes, pipe-laying, ROV and other essential offshore modules. The largest Offshore Construction Vessel today proves to be the Allseas’ Pioneering Spirit built in 2016. She is a gigantic catamaran measuring 382 metres in length and 124 metres in width which is the size of 6 football pitches; while her cranes can cover the distance of the 8 football fields. The gap between two hulls reaches 122 metres by 59 metres and accommodates another vessel, barge ‘Iron Lady’. Moreover, Pioneering Spirit is able to work as a floatel as it hosts 560 crew members and offshore specialists. At present, she works in the Danich sector of the North Sea in Tyra field recycling drilling rigs there on behalf of Total.
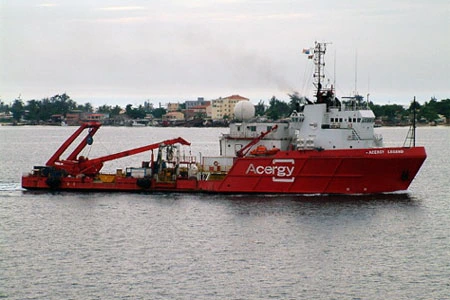
Pipe Laying Vessel
Pipe-laying vessels are among the largest offshore ships. They are used for the installation of the marine pipeline infrastructure for instance from drilling provinces to onshore refineries and so on. Pipelayers usually accommodate an extensive crew of above 100 crew members. There are usually high requirements for the crew as the vessel works in DP mode constantly and is equipped with a heavy-duty crane and sophisticated mechanisms such as ‘S-laying’ or ‘J-laying’ pipe laying equipment.
- The term ‘S-laying’ derives from the shape of the arc piping taken when it’s let up from the vessel to be put in the water. The position of the mechanism aboard the vessel laying out the pipes is completely flat which allows the pipes to take the unique S-shaped curve.
- The ‘J-laying’ pipe laying mechanism is positioned perpendicularly; that enables it to control the curve of the pipe as it is lowered into the required depths of the water and provides the J-shaped curve.
- There is also the technology when the entire pipeline is installed using buoys and tugs; once the pipeline is built and the desired spot reached the buoys are removed and pipeline submerges.